My time at Divers Alert Network has been split between the medical department and the safety services department. On the medical side, we’re working on a research project regarding inner ear decompression sickness in recreational divers. On the safety services side, I’m focused on updating the training materials used by recompression facilities worldwide to better help chambers train their staff. Much of the old material will remain in the updated edition, but I hope to add curriculum from a variety of other sources in the hyperbaric industry, creating a more comprehensive guide than currently available at DAN or other teaching agencies.
Part of this process involves tedious internet searches on the different types of valves, hinges, and piping materials, but a great deal of the research involves hands-on interaction with the various parts of a recompression facility. To accomplish this, DAN organized my visits to the Duke Center for Hyperbaric Medical in Durham, NC, and Bauer Compressors Inc. in Norfolk, VA.
First, going to Duke University’s recompression facility was mind-boggling! We took a tour of the entire facility, including the main chamber floor, control panel, medical rooms, and compressor floor. I have seen other chambers around the country, but nothing compares to Duke in terms of the size, complexity, and expertise available. There are several chambers; each has a specific purpose, maximum operating depth, and possesses unique aspects of engineering. My personal favorite was the golf chamber, which is quite small but can be pressurized to extreme depths far beyond the larger chambers. Studies in this chamber have focused on high-pressure nervous syndrome (HPNS), an issue rarely reported at depths less than 150 meters, so the environment inside this chamber is extraordinarily hostile, to say the least.
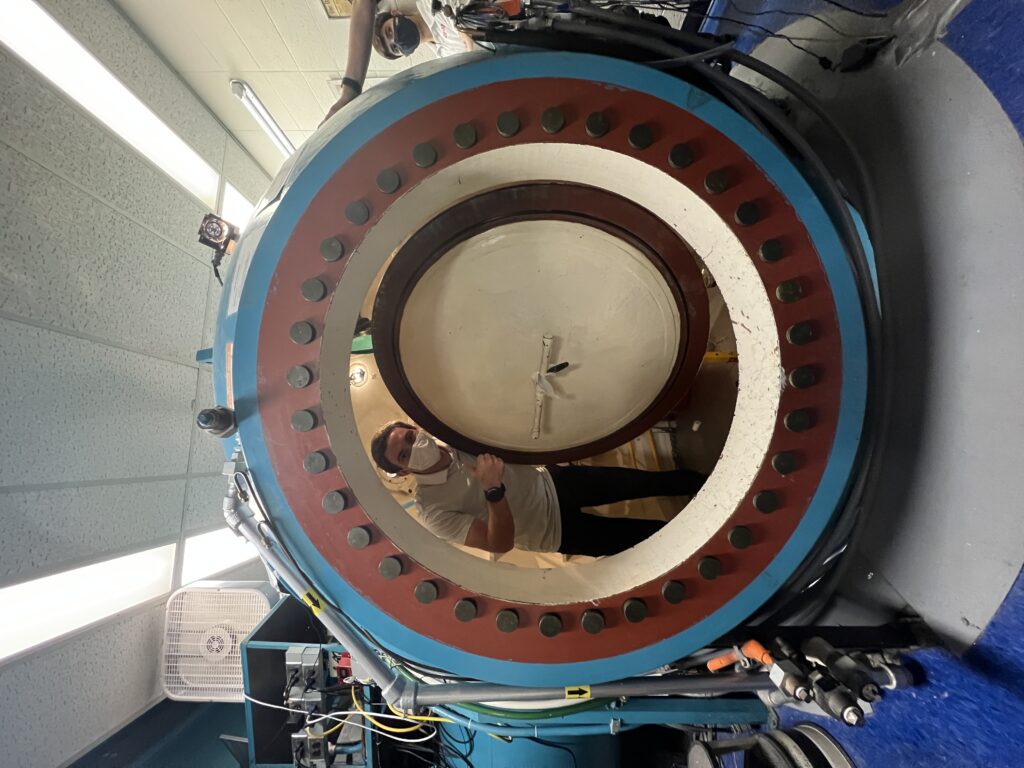
Duke’s “Golf” chamber, where study participants once spent 45 continuous days to evaluate the symptoms of high-pressure nervous syndrome.
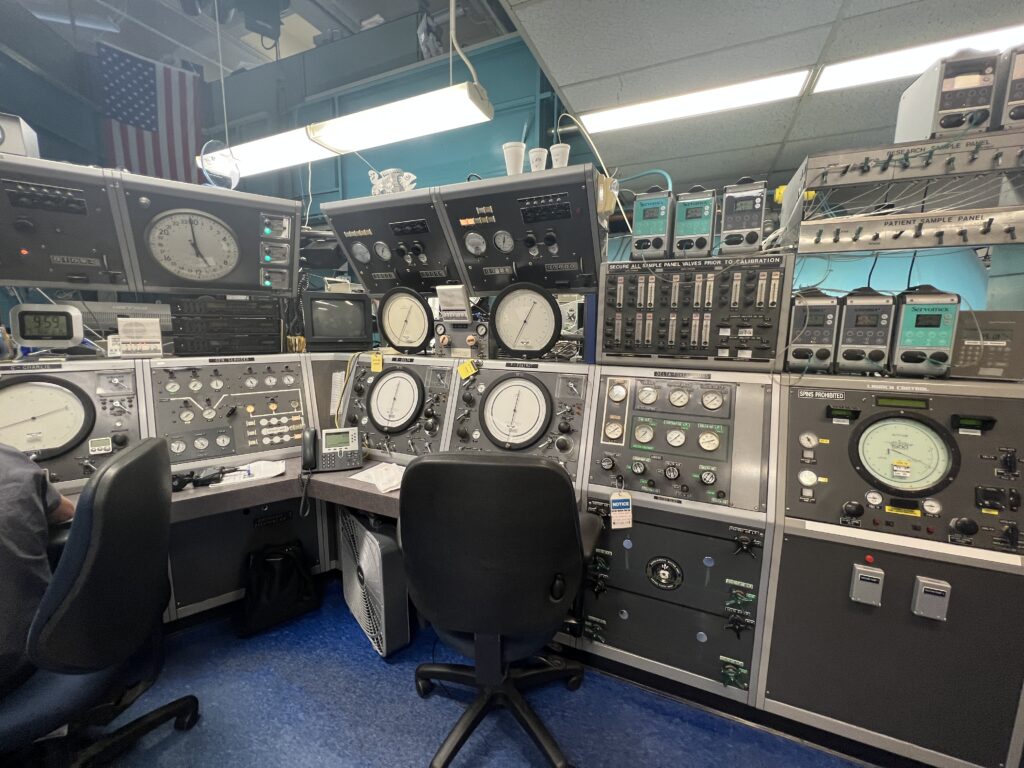
Duke’s main control panel, where chamber technicians and medical staff operate the chambers.
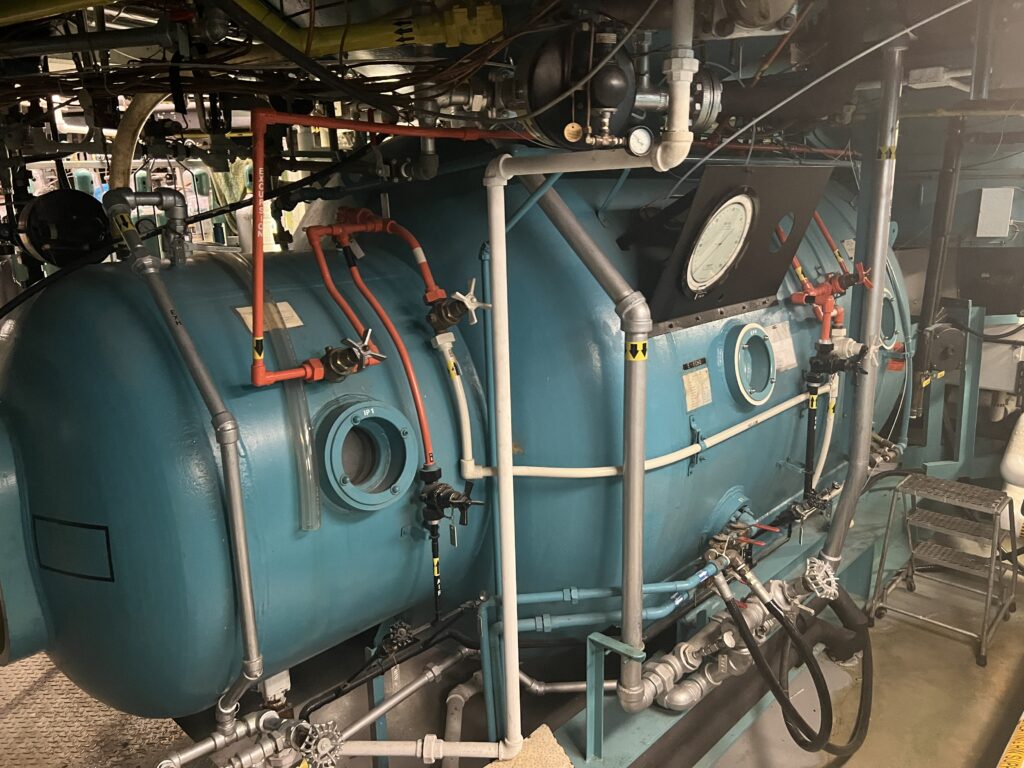
One of Duke’s many chambers. I found this one noteworthy because of its easily visible inlet and outlet piping systems, along with its fire suppression valves.
Our second stop was at the Bauer Compressor factory in Virginia. I had heard of Bauer because of their long history in the SCUBA/recompression industry, but I was shocked at the size of the factory. They had six large buildings, each containing close to 100 employees (and this was just at their US location). We were able to see the various stages of building a compressor, the detail-oriented engineering, and all the safety features that have made Bauer successful over the last 75 years. One of the highlights was their new filling station, which can sustain an explosion from a scuba cylinder at over 3000 psi without causing major damage to the dive shop or fill station attendant. I’m not trying to promote any of their compressors over another brand, but I can say that after visiting their facility I was humbled by how much I still have to learn about the engineering side of hyperbaric medicine.
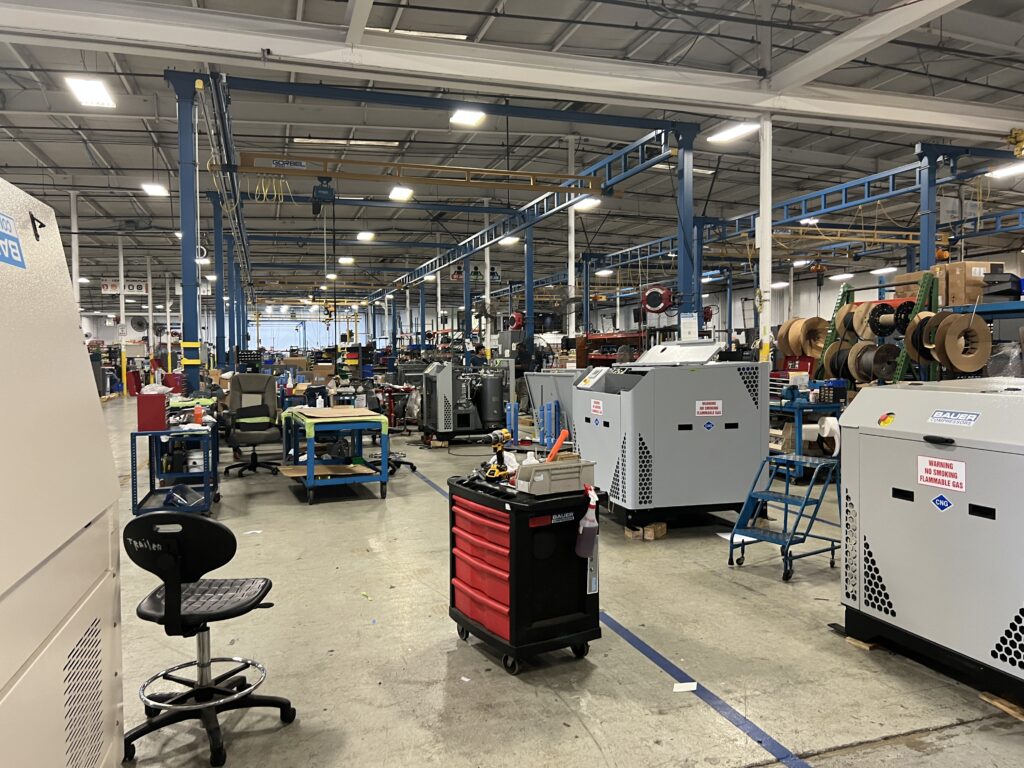
One of the buildings within the Bauer campus

An example of one of the compressors that could be used at a SCUBA shop for filling tanks.
Between the two tours, we were able to see both sides of a recompression facility. While the updates to DAN’s training manual are not specific to certain types of chambers or compressors, having a better understanding of them allowed me to make more specific changes to the protocols. Right now, my focus has been solely on the chamber operator manual, but I’m hoping to also work on the chamber attendant manual and the chamber toolbox in the future.
Once the edits are completed, the plan is to divide the manual into two editions; a longer form will remain in print while a shorter version will be uploaded to DAN’s eLearning site. Looking beyond the scope of my internship, DAN intends to translate the manual into several languages so recompression facilities around the world are able to adequately train new staff. Overall on my end, however, the project has been a great way to learn more about the engineering aspects of recompression facilities, and the importance of safety protocols to prevent accidents in hyperbaric environments.